Masonry Repair Long Island addresses signs of wear and tear like cracks, chips, and crumbling mortar. It can also involve restoring brick or stone structures to their original appearance.
The easiest type of masonry damage to fix is small indentations. These can be filled with Spackle which is easily purchased at any hardware store. Once smoothed out and even with the wall it should then be sanded and primed.
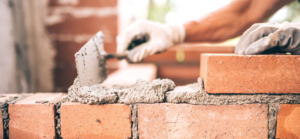
Masonry is the building material that makes up most of our buildings. It involves layering bricks and stone with cement for strength, durability, and aesthetics. It is an incredibly durable construction technique, but even the most sturdy and attractive masonry structures suffer wear and tear over time. The best way to protect the integrity of your building and ensure its appearance is to keep up with regular masonry repair services.
Small cracks and chips in masonry might seem harmless at first, but they can cause more serious issues over time. If they are not addressed, water can seep into the cracks and cause internal damage. Masonry repair work can help you spot and address these issues before they become major problems, keeping your building in its best shape for years to come.
Displacement is another common problem that can affect a masonry structure. This happens when the bricks or stones begin to pull away from each other due to a lack of adequate support. This can be caused by a number of factors, including age, moisture penetration, or the elements. If your masonry is showing signs of displacement, it is important to call in professional masonry repair services immediately.
When it comes to mortar, small cracks or crumbled pieces of brick can be repaired through a process known as tuckpointing. A mason can tuckpoint mortar joints in the bricks or re-mortar a damaged wall, using a color-matched mortar to create a seamless look. The mason will also scrape and clean the surface of the masonry to remove any dirt, debris, or dust that could get in the way of the tuckpointing.
If the masonry is very damaged, it may need to be completely restored rather than just tuckpointing. A mason will evaluate the masonry and determine if it needs to be replaced entirely or if it can be repaired by using a combination of techniques. For example, brick stairs that were built without a concrete footing will not be able to be repaired simply by tuckpointing the existing bricks. In these cases, the mason will need to dig out the old bricks and pour a new set of stairs.
Structural Damage
Masonry is a strong and long-lasting building material, but it’s not immune to the natural wear and tear of time. From minor cracks to structural damage, the foundation of your home or commercial structure needs regular masonry repair to maintain its integrity and appearance.
Masonry structures are susceptible to several common structural issues, including bowed bricks, crumbling mortar, and displacement. When left untreated, these problems can compromise the integrity of the structure and threaten the safety of its occupants. In addition to being an eyesore, structural damage can also reduce the value of your property and cause water infiltration, which may lead to costly repairs or even foundation replacement.
The first sign of a potential structural problem is discoloration in your masonry walls. Staining is a common occurrence in masonry due to water penetration, but can also be caused by aging and weathering. If you notice discoloration, it’s important to contact a mason to investigate the cause and determine whether a repair or replacement is necessary.
Another common sign of a structural problem is spalling brick, which occurs when bricks break down and fall out of the wall, leaving gaps that weaken the overall strength of the brickwork. While this type of masonry damage isn’t as severe as cracks or chips, it’s still a serious issue that requires immediate attention.
If you’re unsure of the difference between repairing and restoring masonry, keep in mind that while repairs involve fixing cracks and chips, restoration involves rebuilding or replacing the damaged brick and mortar. When a masonry expert performs restoration, they are focused on preserving the character and beauty of the original structure while ensuring that it has the structural integrity required to provide protection from the elements.
The foundation of your home or commercial structure is the most important part of your entire building, ensuring stability and security for the occupants. Foundation issues like displacement, lateral support anchors, and bond failure are all dangerous to your family or customers, and must be addressed immediately. Inspecting for signs of deterioration and having professional masonry repairs done regularly are the best way to ensure that your foundation is safe.
Water Damage
Masonry is a type of construction that uses bricks and stones with mortar to create buildings, walls, and other structures. While masonry is very strong and durable, over time it can become damaged or cracked due to natural wear and tear and weathering. When this occurs, a masonry repair expert can repair the damage and restore the structure to its original condition.
The number one cause of masonry damage is moisture penetration. Since brick is porous, it can easily absorb water which can cause cracking, crumbling and other damage. Rain, runoff and other factors can all contribute to this problem and it is crucial that any problems are repaired as soon as they are detected. The best way to prevent water damage is by scheduling regular inspections by a professional masonry contractor and implementing a waterproofing system.
In addition to water damage, masonry is also susceptible to erosion and other types of natural disasters that can cause significant damage to a building. In some cases, it may be necessary to use a masonry restoration contractor to restore the historical integrity of the building and to make any repairs that are required.
Another issue that often requires a masonry repair specialist is the development of efflorescence on a masonry surface. This is a white, chalk-like substance that forms on the surface of a masonry wall and can be quite unsightly. It is a result of the leaching of water and can occur on both exterior and interior masonry surfaces. The removal of this substance should only be performed by an experienced mason as it typically involves the use of a very corrosive chemical known as muriatic acid which should only be used by professionals.
While masonry is a very strong and durable material, it can be susceptible to damage over time. Whether it is caused by erosion, flooding, or other natural disasters, the damages to a building can be very severe and can lead to serious safety issues for those who live in or work in the structure. It is important to hire a professional commercial masonry repair company as soon as possible when any signs of damage are seen to ensure the integrity of the building is maintained.
Efflorescence
While brick and masonry are known for their durability and longevity, structures built with these materials aren’t immune to damage and failure. While many signs of masonry damage are quite obvious – crumbled bricks, missing mortar and collapsed chimneys – some symptoms may be more subtle, such as the formation of white crystalline deposits on the surface of your masonry wall. This chalky deposit, called efflorescence, isn’t only unsightly but also a sign of moisture problems that require immediate attention.
Efflorescence forms as naturally occurring mineral salts are transported from inside the masonry substrate to the surface through water. The water then evaporates, leaving behind the salts on the surface of the masonry. The process is most common in new construction, but can occur at any time after a masonry structure has been exposed to the elements. The amount and character of efflorescence depends on the nature of the soluble salts in the building material and atmospheric conditions.
The crystalline deposits can appear on concrete, brick or stone surfaces. They are usually white, but can be yellow or brown depending on the type of salts present in the masonry. Efflorescence is often confused with rust, but the two are different, as rust only occurs after iron compounds are oxidized, while efflorescence is caused by water-soluble salts.
There are several ways to prevent or treat efflorescence. Using a clear waterproof sealant to the surface of masonry can prevent it from forming in the first place. Adding a capillary break to your building envelope can also minimize the movement of water within masonry materials, decreasing the chance of salts being brought to the surface.
Efflorescence can be a serious problem for a homeowner or commercial property owner. Despite the fact that it is a natural part of the aging process, it can lead to structural damage and lead to further moisture problems. It is important to identify the source of the moisture, so that the problem can be repaired and prevented.
Efflorescence can be removed with the use of cleaning solutions. However, these chemical cleaners can be corrosive to the brick or masonry, and they should be used with caution. Another option for removing efflorescence is light (brush) sandblasting. However, this treatment can erode the surface of masonry and expose coarse aggregate, so it should be used with caution.