Concrete Repair Eau Claire is necessary when it becomes apparent that a concrete structure is not in good condition. It is important to recognize and address problems early to prevent them from becoming major issues.
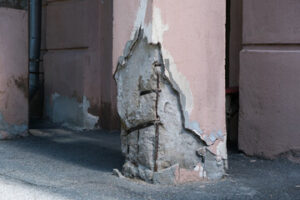
Depending on the type of damage, different repair methods can be used. Choosing the right products is essential to ensure the success of your repairs.
Cracks
Concrete cracks are one of the most common problems that we see in concrete repair. These can range from a cosmetic concern to structural issues that could threaten the safety of a structure or its occupants. There are many causes of concrete cracking, including freeze-thaw damage, strain from slab settling or impact trauma. While the occurrence of cracks does not necessarily indicate that a foundation needs to be replaced, it is important to address them as soon as they are discovered in order to prevent further damage and to minimize the risk of injury to occupants.
If the cracks are minor, they can be repaired using a standard concrete repair material such as dry cement or mortar. It is important to properly prepare the concrete before applying the repair product. This includes cleaning the area around the cracks with a pressure washer to remove any dirt or debris that may be present. It is also important to spray the cracks with water prior to applying the repair material to ensure that the existing concrete is hydrated and able to bond to the repair material.
It is also important to choose a quality concrete repair product that is suitable for the type of damage that you are repairing. Different types of damage require different repair techniques, and it is critical to use the right products in order to ensure a long-lasting, effective repairs. This is particularly true with concrete crack repairs, as the proper preparation and selection of a repair method can make the difference between a crack that lasts for years or a crack that fails within two years.
Aside from the potential injury hazards caused by cracked concrete, it is also important to note that a damaged concrete surface can detract from the appearance of a building or its surrounding landscaping. Especially in a commercial setting, a cracked concrete surface can reflect negatively on a business and its image.
If the damage to a concrete surface is extensive, it may be necessary to replace the entire unit. This is a more costly option than repairing it, but it may be the only way to restore safety and aesthetic appeal to a structure.
Leaks
Slab leaks are one of the most dangerous and difficult types of concrete repair to address. Because they occur underneath the concrete foundation or slab of your home, these pesky leaks can cause serious damage to living spaces without you even knowing it. Fortunately, there are a few things you can look out for to catch slab leaks in the making.
Moisture spots on walls and floors in your home may not seem like a huge deal at first, but they can be an early warning sign of a slab leak. If you see moisture on the floor, walls, or carpets around a window (even after checking to make sure all faucets are turned off), this could indicate that water is seeping from pipes into your living space.
Leaks from water, sewage, or gas lines are more common in older homes with copper or galvanized steel pipes. These pipes are more prone to corrosion than their PVC counterparts, and can also be affected by outside pressure from earthquakes, underground streams, or soil erosion. The leaks are caused when the pipes rub against each other, which causes abrasion and wear that can eventually weaken them.
If you notice a significant drop in your home’s water pressure, this can be a sign that there is a leak under your concrete slab. These leaks can be a serious problem, and can cause your foundation to crack over time.
To fix a slab leak, you will need to cut into the concrete slab to access the leaking pipe. This can be a messy job, so it’s best to hire a professional to do the work for you. This will minimize the amount of dust created in your home, and will ensure that the repairs are done correctly.
Before you start cutting into your concrete slab, you will need to prepare the area. You will need to chip away the top layer of the concrete to expose the leaking pipe, then dig down at least 8 inches into the soil. This is the only way to be sure that your leak will be repaired properly.
Loose Joints
Concrete expansion joints are cut in concrete slabs or the joints between concrete slabs that act as shock absorbers to help concrete expand and contract as the temperature changes. When these expansion joints deteriorate or are not properly repaired, it can cause the adjacent slabs to crack. Expansion joint repair is a relatively simple task that should be done on an ongoing basis to avoid concrete slab damage.
Early thermal contraction cracking is caused by rapid changes in temperature which causes the cooler surface of the concrete to shrink faster than the underlying concrete, thus creating stresses that are greater than the concrete’s tensile strength. These cracks typically appear in the form of hairline cracks that extend from the surface to mid-depth in the concrete. These cracks can be minimized by avoiding excessive heat of hydration, reducing restraint where possible and providing reinforcement steel at optimum spacing.
Long-term drying shrinkage cracking is a result of the concrete drying and losing moisture to the point where it begins to craze or develop surface bubbles. It is caused by a variety of factors including: the amount of water and cement used, aggregate size, concrete mix design, the use of admixtures and inefficient curing. Long-term drying shrinkage cracking is most common in thin floor slabs and walls.
Expansion joints in concrete are filled with a special material to allow the concrete to move as it expands and contracts, but this material can break down over time, which allows the adjacent concrete to crack. These loose expansion joints can create trip points in the concrete and require frequent repairs.
To prevent this, expansion joints should be kept sealed and properly maintained. This can be accomplished by using a high-quality, long-lasting product that dries to a solid, flexible seal, sticks to anything and resists weather conditions. One of the best products to use is a self-leveling joint filler that is available at any home improvement store, called Sikaflex.
Taking steps to repair cracked expansion joints the minute you notice them is not only safer for your warehouse workers, but cleaner and more economical for your products as well. It’s a much better option than replacing entire concrete floors, so don’t procrastinate and call for a professional to fix your expansion joints the moment you see any damage.
Scaling
Scaling is the local flaking or peeling away of the near surface portion of concrete or mortar. It exposes the coarse aggregate and can lead to further distress such as spalling if not addressed. Scaling is caused by hydraulic pressures created by the expansive forces from repeated freeze-thaw cycles within the concrete. This is exacerbated by deicing chemicals, which increase both the saturation of the concrete and the number of freeze-thaw cycles. Scaling can occur on a very localized basis or may expand to larger areas of the structure.
Preventing scaling requires the use of a high-quality mix of concrete, strengthening fibers, and an integral/topical sealer. This will help to protect the concrete from harsh chemicals and freezing conditions that can cause the concrete surface to deteriorate. It is also important to regularly clean the concrete surfaces and to remove any foreign materials that can contribute to the development of a softer or weaker concrete surface.
The most effective way to repair concrete scaling is by using a liquid bonding material that will penetrate the existing concrete and strengthen it. The bonding material can be applied by brush, sprayed, or poured. Once the bonding agent has been properly applied, it is important to follow recommended curing methods to allow the resurfacing material to hydrate fully.
For small scale repairs, a concrete patching product that can be hand-placed is typically preferred. These products are made from a high-strength concrete that is designed to be mixed with water to provide the strength needed for the repair. They will also contain reinforcing fibers to help reduce the risk of further damage from shrinkage or movement of the concrete element.
For large-scale repairs, a pre-mixed bagged product is often the preferred option. These products are usually produced in a factory with strict quality control guidelines, and are designed to perform on a like-for-like basis with the existing concrete structure. These products will often be certified by an independent testing agency to ensure they are of the highest quality. In addition, they will be formulated with a reduced amount of water to minimize shrinkage and to promote hydration for maximum durability.