3D Printing (or additive manufacturing) creates physical parts by constructing them layer-by-layer. This process contrasts with subtractive and formative manufacturing methods such as CNC machining or injection molding.
It reduces lead times from weeks to just a few hours, helping product designers and manufacturers bring new products to market faster. Contact By3Design now!
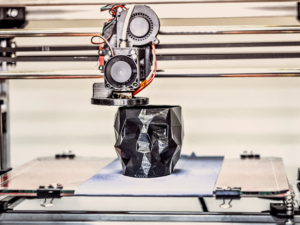
3D Printing is the most advanced prototyping process currently available, allowing product designers and engineers to create functional prototypes that look and feel like the finished product. The process utilizes layer-by-layer fabrication to turn digital CAD models into tangible physical objects. It eliminates the need for expensive tooling, and it’s much cheaper on a per-part basis than traditional processes, such as injection molding. This allows for rapid iterations, saving time and money.
In addition to speeding up development and reducing costs, 3D Printing is also a great solution for low-volume manufacturing, often referred to as “rapid manufacturing” or “small batch custom production.” Companies can print spare parts, tools, jigs, fixtures and end-use parts, enabling them to reduce inventory, improve service, and shorten design and production cycles. This has been especially beneficial for automotive manufacturers, which have been using 3D printers for years to print spares and jigs, but are now also turning to 3D Printing for on-demand production of end-use parts.
Before commercial 3D Printing, engineers used hasty foam mockups or detailed clay models crafted by skilled artisans. These processes were not only slow but they also required high fabrication costs for each prototype, limiting the number of iterations they could make in a given timeframe. With the advent of 3D Printing, engineers can now create a proof-of-concept prototype in hours and have a functional prototype for testing within days.
This can drastically cut down on the number of changes required to go from concept to a functioning prototype and prevents businesses from making costly mistakes that would be impossible to fix once a project goes into production. It’s also a great way to test and validate a new design and to communicate the engineering intent to the production team before investing in expensive tooling.
Another great use for rapid prototyping is to develop a physical test fixture for a specific application. For example, NoiseAware, a maker of noise-level monitoring devices, used their 3D printer to produce a functional prototype of their product and save money on a custom made fixture. The company was able to save on the cost of the fixture and the time that it took them to get the part, which prevented them from going to market with an untested product.
Design Flexibility
3D Printing has a remarkable ability to create complex geometries that wouldn’t be possible with traditional manufacturing methods. It also offers greater flexibility with materials, including flexible plastics for consumer products and rigid metals used in aerospace and automotive. In addition, 3D Printing can produce a much smaller amount of waste material than traditional construction methods. Moreover, it is environmentally friendly as the raw material (such as Polylactic Acid) used in the process comes from renewable resources, such as corn starch or sugarcane. Moreover, the process can be done locally, which significantly reduces freight costs and associated emissions.
Prototyping with 3D Printing allows designers and engineers to test ideas in the marketplace quickly and effectively. This means more design integration and faster improvement, transforming product development into a continuous cycle of testing, learning, and adapting.
This flexibility in design and production also has profound implications for the world economy. In addition to reducing costs and increasing productivity, it helps companies diversify their portfolio of products by eliminating the need for large inventories. This, in turn, limits the financial risk of price fluctuations and market volatility. It also eliminates the need to pay taxes and tariffs on finished goods because they are being shipped directly to end users.
The technology can also make local manufacturing cost-competitive with overseas operations. It can also limit the risk of political instability or natural disasters that may occur abroad. Moreover, the ability to print any part anywhere on demand enables manufacturers to flexibly respond to fluctuating local demand without having to stock large quantities of a single product.
However, the flexibility offered by this revolutionary technology has also posed challenges to the legal system. When designs can be teleported instantly, it poses new legal challenges related to intellectual property, copyright infringement, and international trade and customs. As a result, businesses must rethink their business models and adapt to these changes. Regardless of the challenges, this is a game-changing technology that is poised to transform the global economy.
Cost-Effectiveness
Compared to traditional manufacturing, 3D Printing is cost-effective for low-volume production and highly customised products. This is due to the elimination of upfront investment required for tooling and molding and the reduction of labor costs associated with assembling parts. It also reduces the cost of shipping and warehousing.
Moreover, unlike traditional manufacturing processes that use subtractive methods, which produce significant waste material, 3D printing technology generates minimal waste. This saves on materials and energy costs as less plastic is used for each print. This process is also more efficient because it requires fewer operations, and machine set-ups are shortened, which reduces operation expenses.
Furthermore, since 3D printers can be operated on a contract basis, companies can avoid expensive overhead and capital investments. These are typically required for other technologies such as injection molding, CNC milling, and metal casting. This significantly reduces initial project risks and allows for more flexibility and agility in product design, minimizing the need for redesigns and costly changes to production processes.
In addition, the ability to 3D print spare or replacement parts on demand reduces warehousing and inventory costs. Several of UltiMaker’s customers operate on a “take one, make one” policy and keep a small amount of spare parts on hand to cut down on the need for purchasing from external suppliers.
As mentioned above, the size and complexity of a 3D-printed object influences the final cost. A larger or more intricate print will require more raw material and take longer to print, resulting in higher cost.
The quality of a printed part can also influence the price. Using software to optimize designs for structural integrity and print speed can decrease printing costs. Additionally, lowering the infill percentage can lower material usage while still providing adequate strength.
Post-processing and assembly costs are also factors that can increase the price of a part. For example, sanding, painting, and assembling multiple parts can add significantly to the overall cost. Additionally, the complexity of the design can influence printing time and the need for support structures.
Regular maintenance is also important for reducing printing costs. Insufficient maintenance or a printer in disrepair can lead to wasted raw materials and lost production time, both of which will have an impact on the overall cost. Keeping a printer well-maintained and up to date with the latest software and hardware upgrades can help reduce these costs.
Time-Saving
As 3D Printing becomes more functional and precise, it has become a key tool for businesses looking to improve processes and ramp up development quickly. 3D Printing provides a low-risk, low-cost and fast method of prototyping, which can be used to quickly test prototypes for functionality or to create replacement parts to repair existing machinery or equipment.
With traditional manufacturing methods, you would need to send mock designs to a professional prototype developer to convert them into a functional proof of concept, which can take days or even weeks. 3D Printing allows you to print your own prototype directly from the CAD model, which means you can make iterations much faster and cheaper.
The speed of your 3D printer and the thickness of each layer are crucial factors in determining how long it takes to print your part. You can speed up your print time by increasing your printer’s printing speeds in the slicer settings, but be cautious not to push it too far, as it can risk sacrificing print quality. Another way to reduce your print time is to decrease the print layer height. This will allow your printer to build layers faster, but will result in visible layer lines and lower detail.
One last way to cut down on your print time is to use less support material. This is the material that supports a model as it prints, and is typically only required for areas of the print that are not in contact with the build plate. You can do this by reducing the number of support columns in your slicing program or by using a more flexible material that requires less support material.
Another way to save time is to use the slicing software features that automatically remove support material from the finished print. This can significantly reduce the time it takes to clean up your finished print. You can also reduce the time it takes to print by reducing the thickness of each layer, which can be done by changing your print settings in the slicer.
Finally, if you’re in a rush to finish your print, you can try lowering the temperature of your printer, which will speed up the process by reducing the amount of heat the machine generates. If you’re still pressed for time, you can also check out a local “lab” or workshop where people often work on projects that are too large or difficult to do at home. Some of these sites have various projects that reuse and recycle waste from 3D Printing, turning it into stylish furniture and other goods.